Статьи и описания
Тел. (495) 744-11-17Моб., WhatsApp, Telegram
+7-985-226-12-33
zakaz@faneramm.ru
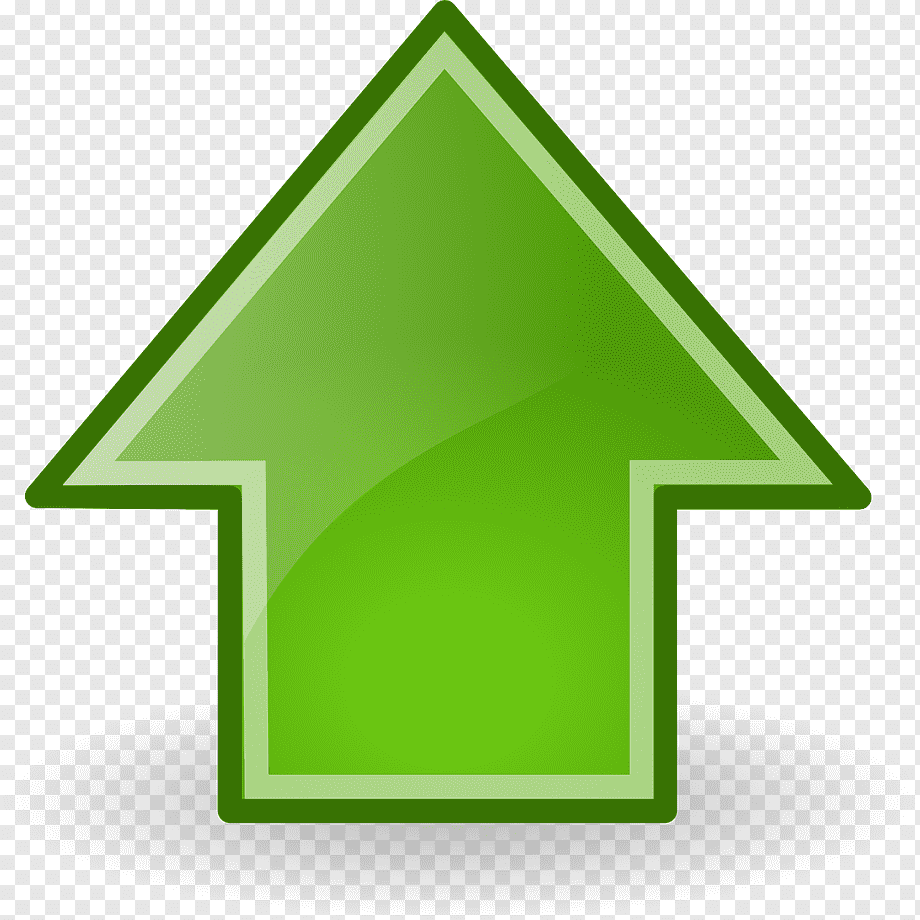
Для организаций просьба присылать заказ на эл.почту в свободной форме
Например:
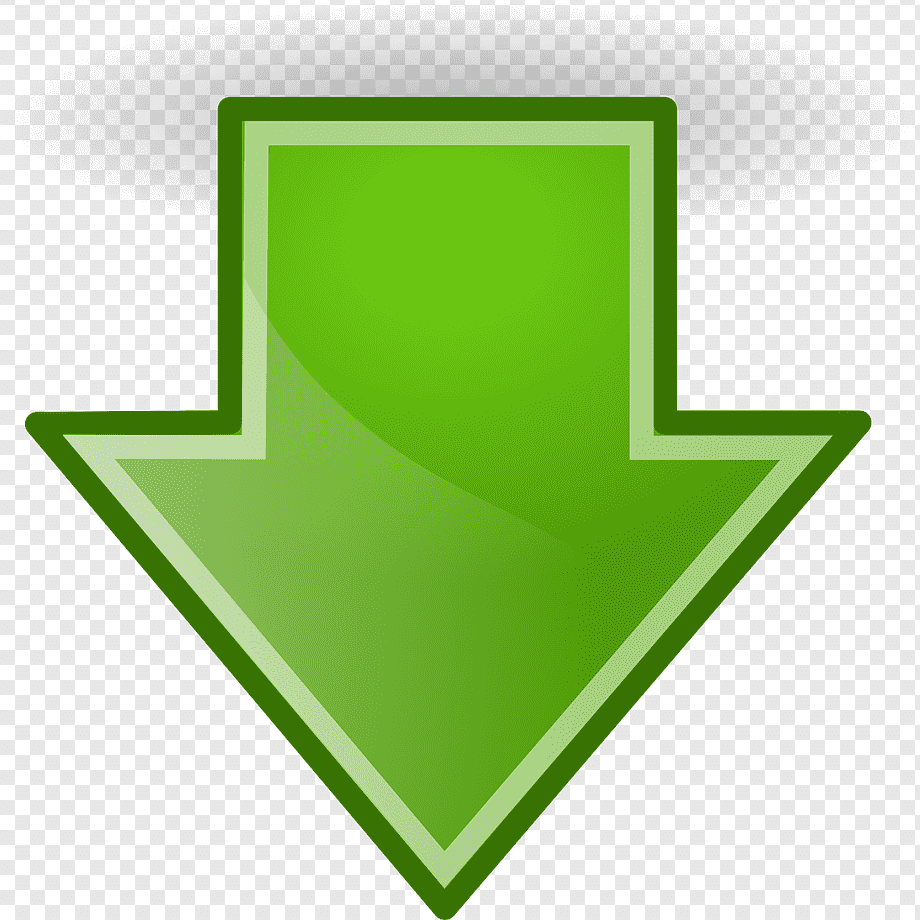
- Нужна Фанера 2500х1250х9 - 35 листов
- Посчитать доставку: указать адрес
- или написать слово: самовывоз
- Указать название организации и Ваши контактные данные
- Приложить реквизиты организации
Купить фанеру 9 мм 2500х1250 мм - присылайте Ваши запросы, уточним цены, скидку, наличие и все оперативно посчитаем
Методы изготовления фанеры
Все существующие методы производства фанеры
Фанера — это многослойный древесный строительный материал, который изготавливается путём склеивания слоёв шпона. Она широко используется в строительстве, производстве мебели, упаковки и других отраслях.
Существуют два основных метода изготовления фанеры: холодный и горячий. Они отличаются температурой прессования слоёв шпона, что влияет на прочность и влагостойкость материала. Холодный метод прессования происходит при комнатной температуре, а горячий — при повышенной температуре. Фанера, изготовленная горячим методом, обычно более прочная и устойчивая к влаге. В процессе производства фанеры также используются различные клеевые составы, которые могут влиять на экологичность и безопасность материала. Современные технологии позволяют использовать экологически чистые клеи, что делает фанеру более безопасной для здоровья человека и окружающей среды. Контроль качества на каждом этапе производства обеспечивает соответствие фанеры стандартам и нормативам. Тестирование готовой продукции позволяет убедиться в её прочности, влагостойкости и других характеристиках. |
![]() |
Методы производства фанеры
Лущение и склеивание слоёв шпона.
Это основной метод производства фанеры, который включает в себя несколько этапов:
- Выбор древесины: для производства фанеры обычно используются берёза, сосна, лиственница, дуб и другие породы дерева. Древесина должна быть здоровой, без гнили, трещин и других дефектов.
- Окорка: с древесины снимают кору, чтобы предотвратить загрязнение шпона.
- Лущение: бревно вращается вокруг своей оси, а специальный нож срезает тонкий слой древесины (шпон). Этот процесс повторяется до достижения требуемой толщины шпона.
- Сушка: шпон высушивают в сушилках, чтобы удалить из него влагу. Это необходимо для того, чтобы фанера была прочной и не деформировалась при склеивании.
- Сортировка: шпон сортируют по качеству, размеру и толщине. Отбракованные листы используются для изготовления других материалов.
- Склейка: листы шпона укладывают друг на друга так, чтобы направление волокон соседних слоёв было перпендикулярным. Затем их склеивают под прессом с использованием специальных клеёв.
- Прессование: фанеру прессуют под давлением, чтобы обеспечить прочность и стабильность материала.
- Обрезка: готовую фанеру обрезают до нужного размера и упаковывают для транспортировки и хранения.
Этот метод позволяет получить прочный и долговечный материал, который широко используется в строительстве, производстве мебели и упаковки.
Холодный метод прессования.
При этом методе склеивание слоёв шпона происходит при комнатной температуре. Он включает следующие этапы:
- Подготовка сырья: древесину окоривают, распиливают на чураки, гидротермически обрабатывают и лущат на шпон.
- Сушка и сортировка шпона: шпон сушат, сортируют и укладывают в стопки.
- Склейка: слои шпона смазывают клеем и укладывают один на другой. Количество слоёв зависит от назначения фанеры.
- Прессование: стопку шпона прессуют холодным способом под давлением 1,8–2,5 МПа.
- Обрезка: готовую фанеру обрезают по формату.
Холодный метод прессования обеспечивает высокую прочность и влагостойкость фанеры, но требует больше времени на производство.
Горячий метод прессования.
В этом методе склеивание слоёв шпона происходит при повышенной температуре. Он состоит из следующих этапов:
- Подготовка сырья и шпона аналогична холодному методу.
- Нанесение клея: шпон смазывают фенолформальдегидным или карбамидным клеем.
- Сборка пакетов: шпон собирают в пакеты, количество слоёв зависит от вида фанеры.
- Подпрессовка: пакеты прессуют для удаления воздуха и равномерного распределения клея.
- Горячее прессование: пакеты загружают в пресс и прессуют при температуре 120–150 °C и давлении 1,8–4,0 МПа.
- Охлаждение: после прессования фанеру охлаждают до 60 °C.
- Выдержка: фанеру выдерживают в течение 24 часов для завершения процесса склеивания.
- Обрезка и упаковка: готовую фанеру обрезают и упаковывают.
Горячий метод прессования позволяет получить фанеру с высокой прочностью и устойчивостью к влаге, которая широко используется в строительстве и производстве мебели.
Сравнительный анализ методов изготовления фанеры
Холодный и горячий методы прессования
- Подготовка сырья: В обоих методах подготовка сырья включает окорку, распиловку на чураки, гидротермическую обработку и лущение на шпон. Однако, в зависимости от выбранного метода прессования, могут быть небольшие различия в подготовке.
- Склейка: При холодном методе склеивание слоёв шпона происходит при комнатной температуре, а при горячем — при повышенной температуре. Это влияет на прочность и влагостойкость фанеры.
- Прессование: Холодное прессование происходит под давлением 1,8–2,5 МПа, тогда как горячее прессование осуществляется при температуре 120–150 °C и давлении 1,8–4,0 МПа. Горячее прессование обеспечивает более высокую прочность и устойчивость к влаге.
- Охлаждение и выдержка: После прессования фанера охлаждается до 60 °C, затем выдерживается в течение 24 часов для завершения процесса склеивания. Эти этапы важны для обеспечения качества фанеры.
- Обрезка и упаковка: Готовые листы фанеры обрезаются до нужного размера и упаковываются для транспортировки и хранения. Оба метода требуют обрезки и упаковки, но качество продукции может различаться.
Горячий метод прессования позволяет получить фанеру с высокой прочностью и устойчивостью к влаге, которая широко используется в строительстве и производстве мебели. Холодный метод обеспечивает высокую прочность и влагостойкость, но требует больше времени на производство.
Холодный метод прессования фанеры
Описание метода:
- Подготовка сырья: древесина окоривается, распиливается на чураки, подвергается гидротермической обработке и лущится на шпон.
- Сушка и сортировка шпона: шпон сушится, сортируется и укладывается в стопки.
- Склейка: слои шпона смазываются клеем и укладываются один на другой. Количество слоёв зависит от назначения фанеры.
- Прессование: стопку шпона прессуют холодным способом под давлением 1,8–2,5 МПа.
- Обрезка: готовую фанеру обрезают по формату.
Этот метод обеспечивает высокую прочность и влагостойкость фанеры, но требует больше времени на производство.
Горячий метод прессования фанеры
Описание метода:
- Подготовка сырья и шпона: сырьё и шпон подготавливаются аналогично холодному методу.
- Нанесение клея: шпон смазывают фенолформальдегидным или карбамидным клеем.
- Сборка пакетов: шпон собирают в пакеты, количество слоёв зависит от вида фанеры.
- Подпрессовка: пакеты прессуют для удаления воздуха и равномерного распределения клея.
- Горячее прессование: пакеты загружают в пресс и прессуют при температуре 120–150 °C и давлении 1,8–4,0 МПа.
- Охлаждение: после прессования фанеру охлаждают до 60 °C.
- Выдержка: фанеру выдерживают в течение 24 часов для завершения процесса склеивания.
- Обрезка и упаковка: готовую фанеру обрезают и упаковывают.
Этот метод позволяет получить фанеру с высокой прочностью и устойчивостью к влаге, которая широко используется в строительстве и производстве мебели.
Сравнение прочности фанеры, изготовленной холодным и горячим методом прессования
Описание методов:
- Холодный метод: склеивание слоёв шпона происходит при комнатной температуре под давлением 1,8–2,5 МПа. Этот метод обеспечивает высокую прочность и влагостойкость, но требует больше времени на производство.
- Горячий метод: склеивание происходит при повышенной температуре (120–150 °C) и давлении 1,8–4,0 МПа. Позволяет получить фанеру с высокой прочностью и устойчивостью к влаге, которая широко используется в строительстве и производстве мебели.
Таким образом, горячий метод прессования обеспечивает более высокую прочность фанеры, что делает его предпочтительным для применения в условиях повышенных нагрузок и требований к износостойкости материала.
Сравнение влагостойкости фанеры, изготовленной холодным и горячим методом прессования
Описание методов:
- Холодный метод: склеивание слоёв шпона происходит при комнатной температуре под давлением 1,8–2,5 МПа. Этот метод обеспечивает высокую прочность и влагостойкость, но требует больше времени на производство.
- Горячий метод: склеивание происходит при повышенной температуре (120–150 °C) и давлении 1,8–4,0 МПа. Позволяет получить фанеру с высокой прочностью и устойчивостью к влаге, которая широко используется в строительстве и производстве мебели.
Таким образом, горячий метод прессования обеспечивает более высокую влагостойкость фанеры, что делает его предпочтительным для применения в условиях повышенной влажности.
Сравнение экономичности фанеры, изготовленной холодным и горячим методом прессования
Описание методов:
- Холодный метод: склеивание слоёв шпона происходит при комнатной температуре под давлением 1,8–2,5 МПа. Этот метод обеспечивает высокую прочность и влагостойкость, но требует больше времени на производство.
- Горячий метод: склеивание происходит при повышенной температуре (120–150 °C) и давлении 1,8–4,0 МПа. Позволяет получить фанеру с высокой прочностью и устойчивостью к влаге, которая широко используется в строительстве и производстве мебели.
Таким образом, холодный метод прессования обеспечивает более высокую экономичность производства фанеры, поскольку требует меньше энергии для склеивания слоёв шпона. Однако фанера, изготовленная этим методом, может быть не такой прочной и устойчивой к влаге.
Перспективы развития технологий производства фанеры
- Автоматизация и роботизация. Внедрение автоматизированных систем и роботов может значительно повысить эффективность производства, снизить затраты на труд и улучшить качество продукции. Это также позволит сократить время на производство и уменьшить вероятность ошибок.
- Использование новых материалов. Применение новых видов сырья, таких как композитные материалы или биоразлагаемые пластики, может привести к созданию более экологичных и устойчивых продуктов.
- Улучшение процессов склеивания. Разработка новых клеевых составов и технологий склеивания может улучшить прочность и долговечность фанеры, а также сделать её более устойчивой к воздействию влаги и других факторов.
- Оптимизация процессов сушки. Использование новых методов сушки, таких как инфракрасная сушка или вакуумная сушка, может ускорить процесс производства и снизить энергопотребление.
- Цифровизация и использование программного обеспечения. Внедрение программного обеспечения для управления производственными процессами, оптимизации логистики и анализа данных может повысить эффективность и точность производства.
- Развитие экологически чистых технологий. Поиск способов снижения выбросов вредных веществ и использования возобновляемых источников энергии может сделать производство фанеры более устойчивым и экологически безопасным.
- Интеграция с другими отраслями. Сотрудничество с другими отраслями, такими как строительство, мебельное производство и транспорт, может способствовать разработке новых продуктов и услуг на основе фанеры.
- Исследование и разработка новых форматов и размеров. Создание новых форматов и размеров фанеры может удовлетворить потребности различных отраслей и рынков.
- Обучение и развитие персонала. Инвестиции в обучение и развитие сотрудников могут способствовать повышению квалификации и улучшению качества продукции.
Эти перспективы могут помочь производителям фанеры адаптироваться к изменяющимся требованиям рынка и обеспечить устойчивое развитие отрасли.
Вопросы и ответы
Из чего изготавливается фанера?
Фанера изготавливается из шпона — тонких слоёв древесины, которые получают путём лущения. Для производства фанеры используются разные породы дерева, например:
- берёза;
- сосна;
- лиственница;
- дуб;
- бук;
- клён.
Слои шпона склеиваются между собой перпендикулярно направлению волокон в соседних листах. Это обеспечивает прочность и стабильность материала.
Как делают шпон для фанеры?
Шпон — это тонкие слои древесины, которые получают путём лущения. Этот процесс включает в себя следующие этапы:
- Подготовка сырья. Для производства шпона используются брёвна, которые предварительно очищают от коры и других загрязнений.
- Лущение. Бревно закрепляют на станке и начинают вращать вокруг оси. Специальный нож срезает с бревна тонкий слой древесины — шпон.
- Нарезка. Полученный шпон нарезают на листы нужного размера.
- Сушка. Листы шпона помещают в сушильную камеру, где из них удаляется лишняя влага.
После сушки шпон готов к использованию в производстве фанеры.
Какая самая прочная фанера?
Прочность фанеры зависит от нескольких факторов, включая тип древесины, количество слоёв и способ склеивания. В целом, наиболее прочными считаются следующие виды фанеры:
- Берёзовая фанера. Берёзовая фанера обладает высокой прочностью и жёсткостью, что делает её подходящей для строительства и производства мебели.
- Фанера из лиственницы. Фанера из лиственницы также отличается высокой прочностью и устойчивостью к влаге, что позволяет использовать её в наружных работах.
- Морская фанера. Морская фанера изготавливается из специальных пород дерева, которые устойчивы к воздействию влаги и соли. Она широко используется в судостроении и строительстве.
Выбор конкретного типа фанеры зависит от требований проекта и условий эксплуатации.
Преимущества фанеры
Фанера обладает рядом преимуществ, которые делают её популярным материалом в строительстве, производстве мебели и других отраслях:
- Прочность и жёсткость. Фанера состоит из нескольких слоёв шпона, склеенных между собой. Это обеспечивает ей высокую прочность и жёсткость, что делает её подходящей для использования в несущих конструкциях.
- Устойчивость к влаге. Некоторые виды фанеры, такие как фанера из лиственницы или морская фанера, обладают высокой устойчивостью к влаге. Они могут использоваться во влажных помещениях или на улице.
- Лёгкость обработки. Фанеру легко пилить, сверлить и фрезеровать. Это позволяет создавать из неё различные конструкции и детали.
- Экологичность. Фанера изготавливается из натурального дерева, что делает её экологически чистым материалом.
- Эстетичный внешний вид. Фанера имеет красивую текстуру дерева, которая может быть использована для создания эстетичного внешнего вида конструкций.
Из чего делают гибкую фанеру?
Гибкая фанера изготавливается из шпона, который получают путём лущения. Для производства гибкой фанеры используются разные породы дерева, например:
- берёза;
- сосна;
- тополь;
Слои шпона склеивают между собой с помощью специальных смол и клеевых составов, которые обеспечивают гибкость материала. В результате получается фанера, которая может изгибаться под определённым углом без потери прочности.
Из какого дерева делают фанеру?
Для производства фанеры используются разные породы дерева, каждая из которых имеет свои особенности и преимущества:
- Берёза. Берёзовая фанера обладает высокой прочностью и твёрдостью, что делает её подходящей для строительства и производства мебели.
- Сосна. Сосновая фанера отличается лёгкостью и устойчивостью к влаге, что позволяет использовать её в наружных работах.
- Лиственница. Фанера из лиственницы также обладает высокой устойчивостью к влаге и может использоваться во влажных помещениях.
- Дуб. Дубовая фанера известна своей прочностью и долговечностью, что делает её идеальным материалом для изготовления мебели и напольных покрытий.
- Бук. Буковая фанера имеет красивую текстуру и цвет, что придаёт ей эстетичный внешний вид.
самовывоз со склада![]() |
доставка авто![]() |
доставка 20-т![]() |
манипулятор![]() |
доставка ж/д![]() |
Оптовые предложения фанерных заводов
25.01.25
Завод "Плайтерра"
Ламинированная фанера 9 мм
Размер: 3000х1500 мм
сорт 1/2 F/W (гладкая/сетка)
Цена: 2130 руб/лист